Achieving precise and high-quality TIG (GTAW) or plasma welds can be challenging, especially when dealing with varying material thickness, complex joint configurations, and long weld seams. One of the most effective ways to enhance consistency in TIG welding is by using an Arc Voltage Control (AVC) system. AVC is an advanced automatic voltage control system that ensures optimal arc stability, leading to improved weld quality and increased efficiency.
Applications where welding is close to impossible without AVC:
- Very thin steel sheets – 0,3mm and below, depending on the welding process and clamping type
- Non-round tanks. Common, if they are very thin or incorrectly prepared on a bending machine
- Bent or inclined steel or inconsistently prepared steel (when each weld piece is different)
- Conical or specially shaped weld pieces
- Very small diameter pipes (e.g., exhausts) welded on an automatic seamer. Below a certain diameter, inside backing gas and clamping can be difficult. In some instances, the mandrel bends when clamping.
What is an Arc Voltage Control (AVC) System?
An Arc Voltage Control (AVC) system is a technology integrated into welding automation solutions to regulate the arc voltage and maintain a constant torch-to-workpiece distance. This system automatically adjusts the Z-axis of the welding torch using a precise servo motor based on real-time arc voltage feedback. By dynamically modifying the height of the torch, the AVC system ensures precise arc length control, reducing the risk of defects such as undercut, excessive penetration, or incomplete fusion. AVC also works in pulsed mode.
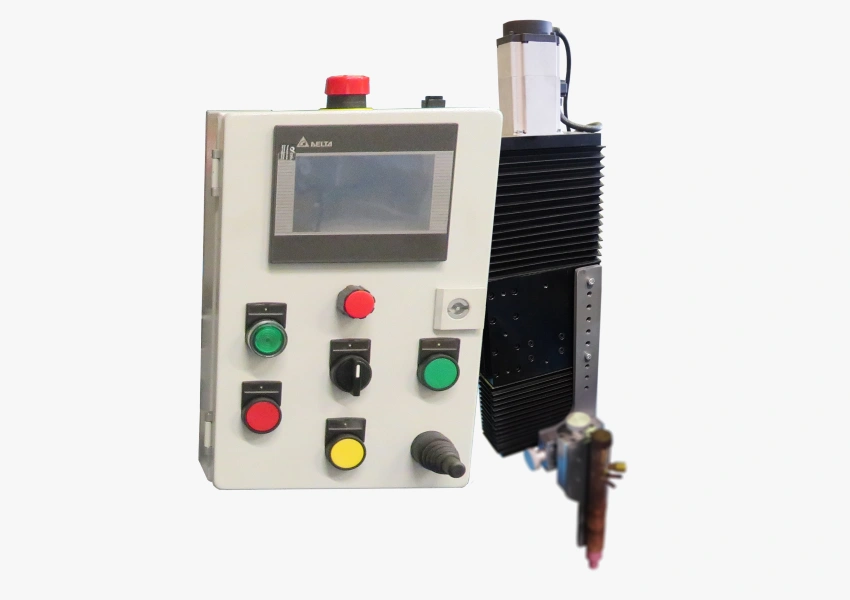
Key Benefits of an AVC System in TIG Welding
1. Consistent Arc Length for Uniform Welds
Maintaining a steady arc gap is crucial for achieving uniform penetration and consistent bead appearance. The AVC system continuously monitors the arc voltage and adjusts the torch height accordingly, eliminating fluctuations that could compromise weld quality.
2. Increased Welding Speed Without Quality Loss
With real-time adjustments, the AVC system enables higher welding speeds while maintaining precise control over arc length. This leads to increased productivity without sacrificing weld integrity, making it an essential feature for industrial TIG welding automation.
3. Improved Weld Quality and Reduced Rework
By maintaining a constant arc gap, the AVC system minimizes the risk of weld defects, leading to higher-quality welds and reducing the need for costly rework or repairs.
5. Compatibility with Multiple Welding Processes
Although most commonly used for TIG welding, AVC can also be applied to plasma welding processes, making it a versatile solution for different applications.
6. Seamless Integration with Welding Automation Systems
The AVC system is seamlessly integrated into AVP welding machines, enhancing automation and ensuring precise control over the welding process. Currently, we only integrate it into our welding seamers, it is not possible to buy it as a standalone system.

How Does the AVC System Work?
The AVC system operates by monitoring the arc voltage in real-time and adjusting the torch height via a servo-operated actuator. The monitoring data is sent or read from the welding source (e.g., Fronius). Below are the core functionalities that contribute to its efficiency:
- Real-time voltage detection – The system continuously senses the arc voltage and makes immediate height adjustments to maintain a steady arc length.
- Servo motor-driven Z-axis control – The torch position is dynamically adjusted based on voltage feedback to ensure consistent penetration.
- Limit switch integration – Prevents excessive torch movement beyond the defined stroke range
- Manual slide options – Provides additional manual adjustability for fine-tuning the torch position when necessary.
Why Choose an AVC System for Your Welding Needs?
For manufacturers and welding professionals looking to enhance precision, repeatability, and efficiency, integrating an AVC system into TIG welding automation is a game-changer. Whether you’re working with stainless steel, aluminum, or exotic alloys, maintaining the correct arc length is critical for achieving superior weld quality.
At AVP, our welding machines can be equipped with advanced Arc Voltage Control systems that streamline the welding process, reducing operator fatigue while improving productivity. If you’re looking for a reliable TIG welding arc control solution, our AVC-integrated machines provide a significant advantage in achieving consistent and high-quality welds.
You don’t have to believe us – visit us and we will show you.
Implementing an Arc Voltage Control (AVC) system in TIG welding automation ensures superior weld consistency, speed, and efficiency. By automatically regulating the torch height based on real-time voltage feedback, the AVC system eliminates variations that can compromise weld integrity. Whether you’re looking to enhance production speed, reduce weld defects, or improve overall automation, AVC is the key to achieving the best welding results.
For more information on AVC systems and welding automation, contact AVP today and discover how our advanced solutions can revolutionize your welding processes.