In producing high-performance exhaust systems, where quality and precision are most important, advanced welding techniques are becoming increasingly important. This is especially true when working with materials like titanium and Inconel, which are widely used in the automotive and motorcycle industries due to their unique properties. Only by staying up-to-date with the latest technologies can we remain competitive in the market.
Titanium: One of the best
Titanium alloys offer an exceptional strength-to-weight ratio, enabling the production of lighter and more durable exhaust systems. Using titanium can reduce the weight of an exhaust system by up to 40% compared to steel systems, which contributes to improved vehicle performance. Its resistance to corrosion and high temperatures makes it ideal for high-performance applications.
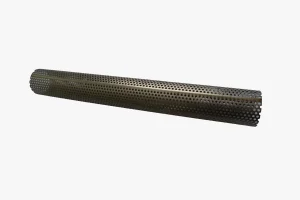
Essential Technology for High-Quality Exhaust System Welding
In 2025, we are encountering the latest technological solutions today almost indispensable for achieving the highest quality welds.
10 Most Common Technologies for Automatic Welding of Exhaust System Pipes:
- Welding cameras (video monitoring, sound monitoring, automatic defect detection)
- AVC system combined with the welding source
- Laser technologies – welding, cleaning
- Regulators for optimization and sensors for shielding gas flow
- Removal of defects (micro-cracks, scratches, etc.) and automatic chemical cleaning of the weld seam
- Cameras with artificial intelligence (AI) for automatic welding position detection, quality control and seam tracking sensors.
- Welding oscillation
- Annealing/tempering of the weld
- Multi-zone gas protection for reduced consumption and trailing gas chambers to prevent oxidation
- Non-magnetic clamping mechanisms to minimize the impact on arc stability
Laser Welding: The Welding Process of the Future
Laser welding is one of the most efficient methods for joining titanium components. The highest quality and repeatability are achieved when the welding source is integrated into automated welding machines. It provides high precision, minimal thermal distortion/deformation, and exceptional weld quality. Laser welding is up to four times faster than traditional methods like TIG welding, significantly improving productivity. While TIG welding still plays a strong role in exhaust system welding due to certain advantages, these are becoming less significant each day.
Additional Benefits of Laser Welding:
- Minimal consumption of spare parts: no need for tungsten electrode grinding
- Height-insensitivity, eliminating the need for AVC systems or other height correction systems
- Reduced heat input: more efficient cooling systems, especially for longitudinal welding
- Integrated oscillation function: covers smaller material defects with beam width setup
- Energy-efficient: 90% of energy is used for welding (compared to only 20% with TIG)
- Reduced impact (effect) of material contamination on the arc
Handheld Laser Welding System of the Highest Quality: IPG
The IPG LightWELD system brings a revolution in handheld laser welding. It is the leading handheld laser welding source, dominating the global market. This portable system is easy to use, quick to set up, and ensures very high weld quality across various materials and thicknesses. With just a few parameters, we can switch between welding aluminium, copper, stainless steel, titanium, and other materials. Additionally, the XR version enables pre- and post-weld laser cleaning, ensuring weld cleanliness and increased productivity.
The advantage of the LightWELD system compared to standard robotic torches, which have been in use for a long time, is its significantly lower cost and the built-in beam oscillation function. For a lower price, it is possible to build a machine with more features, providing a competitive edge. Integration into an automatic welding machine ensures that parameters such as travel speed, power, beam width, and others are synchronized.
AVP d.o.o.: Your Partner in Laser Welding Systems
AVP d.o.o. is the official distributor for IPG Photonics and an integrator of laser welding systems. Over the past decade, there has been a significant rise in automation with laser welding, especially in automatic longitudinal welding machines. Just in the last month, we have produced and delivered two custom automatic machines for high-end exhaust system welding purposes.
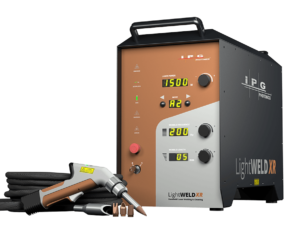
Technical Aspects of Laser Welding
Laser welding involves several specialized solutions that differ significantly from TIG welding to achieve high-quality welds. Key requirements for welding include: protection from oxidation, use of inert gases with precise flow control, regulated pre- and post-welding gas flow, heat input control, and structural integrity of the weld.
Advanced welding techniques, particularly laser welding with systems like IPG LightWELD, open new possibilities in the production of high-performance exhaust systems. By providing precision, speed, and top-notch weld quality, these technologies are setting new industry standards.
AVP d.o.o. offers complete development and production of solutions for welding exhaust systems, pipes, sheets, and other welded parts. Every manual process that we automate brings significant competitive advantages to companies.